Centrale Gelderland Power plant – Explosive Demolition
Brown and Mason Group (BMG) were contracted by the multinational energy company Engie to undertake the decontamination, dismantling and demolition of their Gelderland power plant in The Netherlands. The contract was awarded on BMG’s unappareled experience and involved substantial asbestos removal and extensive use of explosives, all within the timeframe of Brexit, Covid and the war in Ukraine
Centrale Gelderland, a 585MW coal/biomass-fired power plant, including structures 150 Meter high chimney and 95 Meter high boiler house , located in the city of Nijmegen was the first in The Netherlands with a flue gas desulphurisation installation that provided a reduction in sulphur emissions of up to 90%, with the LowNOx burner reducing the formation of nitrogen oxides by 50%. The 1994 constructed DeNox further reduced nitrogen oxides with the use of a catalyst. Large dust collectors and electrostatic filters removed around 99.9% of fly ash particles from the flue gases before they left the plant through the chimney. Engie’s facility had been at the mouth of the Maas-Waal Canal since 1936.
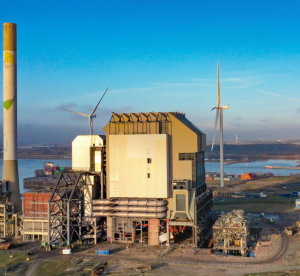
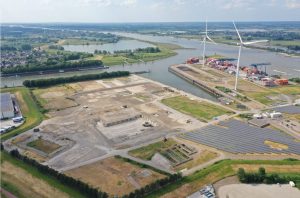
The DeNOx structure collapsed in a westerly direction to allow space for the BH to collapse, LSCCs were used to decouple the structure from the boiler support. The northern support columns were explosively removed, and the bridge section was displaced at a high level, a design solution that reduced the number of explosives with consideration to the heavily mixed industrial and residential estates sited c.165 m south of the structure.
Pre-weakening and use of LSCC, along with the explosive displacement of both main and façade support columns at ground level, allowed the BH to collapse into the space created by the collapse of the DeNOx. The Air-Heater support structure was the final element to collapse due to the concrete construction and not wanting this to interact with the other charged elements. To prevent this structure’s initiation from being disrupted, down-hole delay detonators were used in charging and initiated in advance of the surrounding steel structures.
In addition to the project constraints, the war in Ukraine provided challenges, we could not source the preferred selection of delay detonators and connectors, which led to an already hugely complex design and explosive delay sequence becoming even more complex to ensure we retained the desired timings and collapse mechanisms, class one shipping was cancelled on numerous occasions with priority being given to Ukraine resulting in the LSCC only arriving in Europe with days to spare.
The timing and placement of the kicking charges and LSCC were designed to avoid sympathetic detonation/interference where cut-offs would prevent initiation. The design ensured that peak vibration predictions would not affect the Dyke and the stakeholders.
The project was a huge success, this was the largest and most complex explosive demolition event of a structure in The Netherlands, and a feat undertaken by a British Contractor.